Form 2 3Dプリンター を使ったForm 2 の開発:Formlabs におけるアジャイル開発
- Admin
- 2017年2月13日
- 読了時間: 7分
更新日:2022年3月2日
先日Form2 3Dプリンターを活用したアジャイル開発についてRightHand Robotics社の事例を書かせていただきましたが、今回はformlabs社がどのように3Dプリンターを使ってアジャイル開発をしているか、ひいてはどのようにForm2を利用してForm2の開発を行っているかを書かせて頂きます。
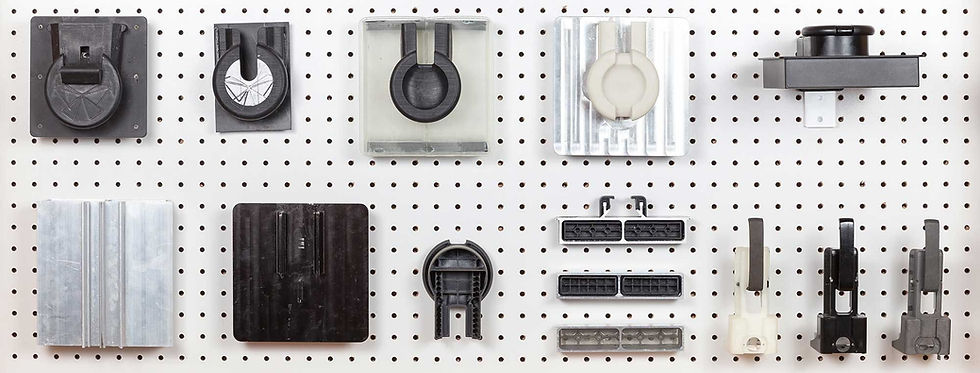
※原文筆者:Adrian Tanner (Fromlabsエンジニア)
製造業は過去10年で飛躍的な進化を遂げてきました。
従来の生産方式では、製品や生産プロセスにおけるいかなる微調整も大幅な再設計、再加工、そして流通の変化を必要としました。
しかし近年は3Dプリント技術の普及と手軽に発注できる工房の存在によって、製造可能性(マニュファクチュアビリティー)重視の製品開発が可能になりました。
3Dプリントされた治具や固定具を使った従来の製造ラインの問題への迅速な対応、さらに大量生産用パーツの直接プリントなどを通して、3Dプリンター技術はアジャイルマニュファクチュアリングの存在を現実に近づけています。
3Dプリンターテクノロジーをフル活用することによって、製造業の新しい時代が始まっています。
Formlabsでは、大量製造前におけるパーツの確認と調整、さらには最終的な製造プロセス自体の改善をデスクトップサイズの3DプリンターForm2をつかって行っています。我々が未来のテクノロジーを形作る全ての段階において、Form2はかけがいのないツールとなっています。

「24時間デザインサイクル」
Formlabsのパーツ製造における社内プロトタイピングは、多くの場合「24時間デザインサイクル」に沿って行われます。
初日にデザイン、夜にはプリント、二日目には片付けとテスト、そして調整。これを繰り返すのです。デザインが安定したら少量のサンプルを回転率の速いショップ(工房)に送ります。テストと調整を素早く繰り返すことによってパーツの信頼度を上げ、パーツ・製品間のコンパティビリティをしっかりと確認することが可能になります。
(3Dプリンター技術を使用することで、デザイン段階における社内でのラピッドプロトタイピングが可能になります。従来の方法だと、工房にデザインを送り、工房がパーツを機械加工するのを待ち、それがまた輸送されるのを待ち、さらにそこから調整を重ね、すべてを繰り返さなければならない。)
パーツのプロタイピングはパーツが生産段階に入ってからも続きます。リアルタイムで調整と確認を繰り返すことで、アジャイルマニュファクチュアリングの強みを最大限に活かすことがでるのです。
「製造ラインにおける3Dプリントパーツ」
治具や固定具を設計した後、二度と修正を加えないという会社も存在します。従来のプロトタイピング方法を使っていては歩留まりの上昇率がコストに見合わないためです。しかし近年の製造業界では、治具の旧式化に伴う再設計や、生産タイム短縮 / 歩留まり率増加のための設計修繕は当前のものとなってきています。
Formlabsの自社プリンター使用工程はプロトタイピングのみにとどまりません。3Dプリントしたパーツは大量生産用カスタム治具にも導入しています。これによって高回転率かつ少量の生産パーツを簡単に、素早く、そして安く生産することが可能になります。
例えば、部品を発注したとしましょう。業者にこちらから指定したスペックは満たしていますが、それでも何かしら問題があり使うことのできないパーツであった、というのはよくあるトラブルです。こういったことが我々にも実際に起きたことがあります。発注していたガラスのパネルケースが準備していた治具に合わなかったのです。その時も我々はガラスに合わせた調整を加え、新しい治具を簡単にプリントすることができました。もう一度発注をして待つ時間や、素材コストといったものを大幅にカットすることに成功したといえましょう。このように、特定のパーツが必要なときは10分CADで設計をするだけで翌日すぐにそれが手に入るのです。
3Dプリントされたパーツは生産プロセスの進化とともに変化することができます。例として、以前我々がアップグレードした治具を紹介しましょう。
下の写真にうつっているのは現在我々が生産ラインで使用している治具の早期プロトタイプです。後処理時間を短縮するために、はじめからビルドプラットフォーム上で(補助ストラクチャを必要とせずに)直接プリントできるようなデザインとなっています。プロトタイプをデザインし、素早く組み立て、何度がテストを行った後、機械加工用に発注し、さらに品質と機能のテストを行い、最終的に委託製造業者の工場へ導入しました。結果、歩留まり率を以前と比べて大幅に改善することができました。

(現在生産ラインで使用されているパーツの初期プロトタイプ)
現在生産されているバージョンはアルミニウム製で、かなり精密な設計が必要となるものなのですが、レジンで3Dプリントされたプロトタイプは精密さを要する作業をなんなくこなし、われわれは実際に金属の型番を作らずとも新しいパーツの評価、調整ができたというわけです。
「3Dプリント治具によるオペレーターのQOL改善」
人間が精密機械を作成するような生産ラインでは、Quality of Life(QOL)がとても大事になってきます。オペレーターが一日に何度も同じ作業を繰り返すということは、当然それらが苦痛であったりひどく鬱陶しいものであったりしてはならないのです。集中力を要する複雑かつ大事な作業工程と、ただ単に面倒で大変な仕事とは区別して考えなければなりません。そして、良い治具はそんな面倒な仕事を楽にしてくれます。

(Form 2のディスプレイスクリーンを固定し、ディスプレイが製品に挿入される以前のオペレーターによる作業を簡単にするための3Dプリントされた治具)
例えば、上の写真の治具は、Form 2に搭載されるディスプレイを(生産ラインにて職員が作業するために)固定するための台です。この装置は製品のテスト中にディスプレイを固定するだけでなく、最終的に外装をかぶせる直前までのオペレーターによるインターフェイス操作を楽にする機能が備わっています。例えば、プリンタカバーの開閉はプリンタカバーに取り付けられている磁石をこのディスプレイの上部で検出して検知するのですが、それがきちんと機能しているかテストする必要が有ります。装置なしではテスト用の磁石を毎回テーピングしなければできないような大変な作業ですが、この治具に嵌め込むだけで確認ができる様になっています。素材コストこそ多少かかりますが、このような装置は生産ラインで働く職員たちの仕事を大いに助けているのです。
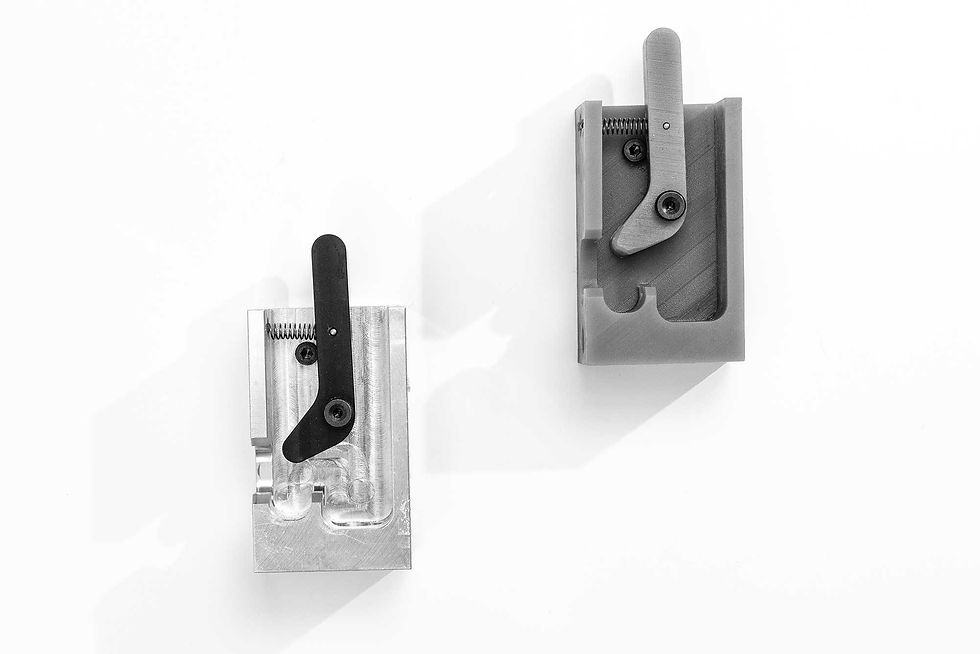
(このアルミニウムとプラスチックのパーツは、3Dプリンターでプロトタイピングを行うことで、品質を確認したうえで生産された。)
テスト用に使うパーツのもう一つの例として、単純なクイックリリースガルバノメーター固定システムがあります。これはSLA3Dプリンターの心臓部であるガルバノスキャナ−の品質をプリンターに搭載する前に確認するためのもので、アルミニウムとプラスチックからできています。プロトタイプは3Dプリンターによって行い、大量に外注する前にサイズやその他の機能を確認しました。このパーツのサイズに関する懸念は少なったものの、スプリング強度に関してはかなりの慎重さが求められました。弱すぎるとガルバノスキャナーを固定することができず、かといって強すぎるとオペレーターが作業しにくくなってしまいます。
これらのパーツを3Dプリンターによってプロトタイピングすることによって、治具の機能だけでなく、操作感まで試したうえでの生産が可能となりました。
「製造業の未来」
今回はFormlabsでの3Dプリンター使用例を紹介しました。これによって3Dプリンター技術が、あなたの会社の製造業にアジャイルマニュファクチュアリングを導入する上での大きな一歩となりうることを理解いただけたかと思います。
3Dプリントされた治具、 固定具そしてプロタイプはFormlabsの多大なる時間と資源の節約につながった上に、最終的にエンドプロダクトの品質向上にもつながりました。3Dプリンティングは、マニュファクチュアビリティー志向のデザインの容易化や製造過程におけるアジャイル性の上昇、そしてカスタムエンドプロダクト生産におけるコストパフォーマンスの向上に直接つながる技術なのです。

Form2 Japan shopでは各種サンプル造形、事業者様向けの出張設置など様々なサービスもご用意しております。材料などのご質問含め右下のチャットもしくは問い合わせページよりお気軽にお申し付け下さい。
Commentaires